– for non-destructive testing of concrete structures
White paper by: Sanat Wagle, PhD, Elop AS Kamal Raj Chapagain, PhD, Elop AS
December, 2020
Introduction
Our modern society is strongly dependent on any means of well-functioning transport infrastructure, including roads, rail, water, and air. Besides this, we expect a reliable energy supply and long-lasting buildings. The most commonly used material for any ground infrastructure is reinforced concrete, and this trend will continue, growing the already enormous global production of concrete even further.
Even though concrete is so common, it is also susceptible to different kinds of deterioration processes and defects, as a consequence of improperly controlled production or construction processes, environmental conditions, cement composition, pollution, and even surrounding infrastructure, amongst other things. Examples of damages that these defects and deterioration processes might lead to are: cracking, reinforcement bond loss, voids, reduction of the cover layer thickness, corrosion, delamination, etc.
In the long run, if existing problems remain unaddressed, they will lower the performance level of the structure and eventually lead to unsafe structures, or even fatal accidents. Preventing that necessitates methods for regular assessment of the structural integrity to avoid problems that might lead to shorter service life. Having said that, maintenance of the asset can not only be planned, but also repairs and interventions can be precisely targeted and localized, retaining structural integrity and extending its lifetime, whilst at the same time ensuring the structure fully fulfils safety requirements. By all means, this has noticeable economic as well as environmental implications.
It is also important to mention both for our well-being and that of future societies is estimated that the construction industry is responsible for up to 40% of global energy consumption (1) as well as up to 40% of all waste creation (2). Furthermore, within the next ten years, the demand for global construction is expected to increase by 70% (3). In the light of these numbers, many have been looking for ways to move the industry in a more sustainable direction.
For a long time, our economy has had an open-ended setup with a linear material flow. In such a traditional setup, the raw materials are utilized to make a product, which at the end of its service/lifetime is disposed of and thrown away. In such an economy, materials end up with very little or no value. This consumes huge amounts of our common resources, making it unsustainable. In the case of concrete materials, this end up as construction debris, with the main application being landfill. However, before this the building may need to be demolished, and debris will need to be transported to the proper place, increasing environmental impact further. In a circular economy model, where extending lifetime and avoiding waste are the main assumptions, all materials are conserved and used as input for new products4. Such a state can be achieved through designing, maintaining, reusing, remanufacturing, refurbishing, and recycling with clear goals in mind.
For existing concrete infrastructure, this implies maintaining and prolonging their lifecycle, rather than replacing it with new builds – if safety and design standards are in place. To be able to extend their lifetime, it is essential to know their health condition. Traditionally, this has been carried out by visual inspections, which limit assessment to investigation of the surface of a structure, bringing any conclusions about internal issues only when the deterioration is already well advanced. The only way to find out about structural problems earlier, has been by the use of the coring technique, which is expensive, time-consuming, and weakens the structure on
which coring is performed even further.
The idea of Non-Destructive-Testing (NDT) assessment is not new and dates back to the end of the nineteenth century, becoming increasingly popular after WWII, with a growing number of techniques used for inspection. However, some of these techniques require immense experience for the proper interpretation of obtained data. Others are complicated, yet not reliable when it comes to the obtained results. Most require a significant workload for both: appropriate data gathering, analysis, and interpretation, as well as providing proper reporting.
Only some of these techniques give the possibility to obtain 3D visualization of the interior structure that leads to a better understanding and detection of possible defects. Also, along with the recent development of smartphone technology and the overall trend of digitalization, some of the commercially available devices allow for more repeatable and productive workflow.
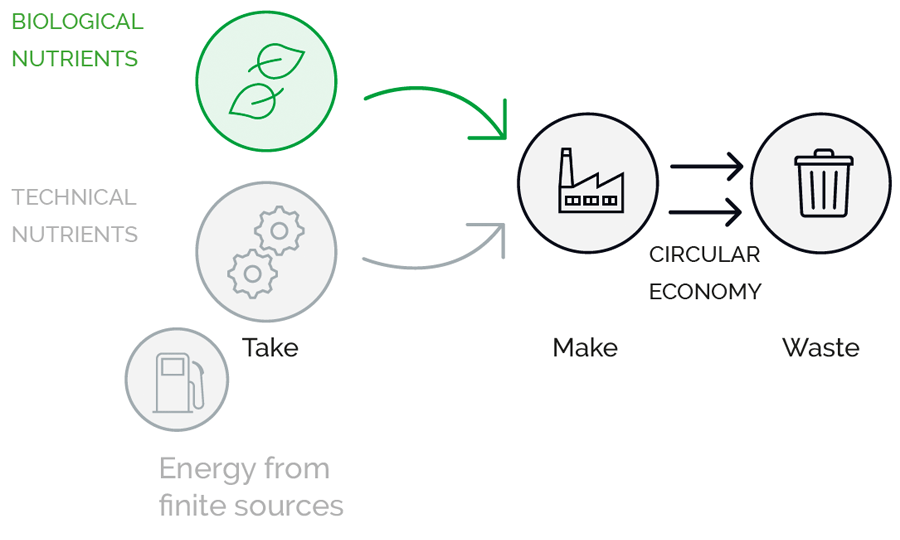
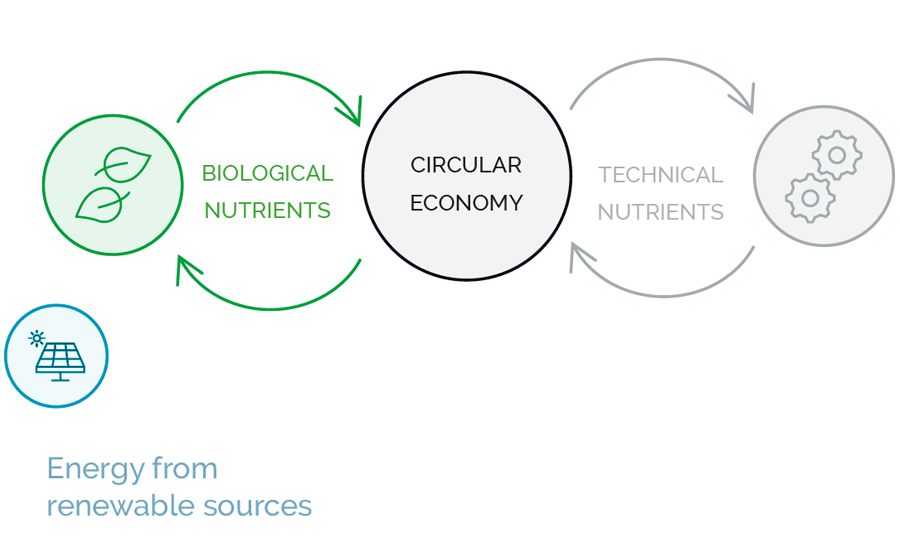
Figure 1:
Linear v.s. circular economy